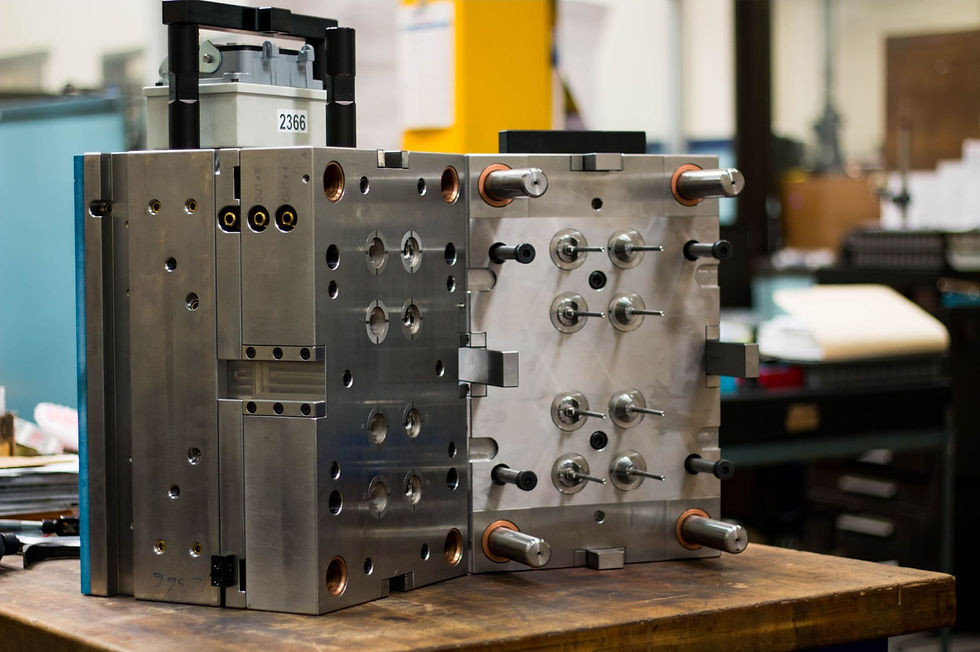
Stellen Sie sich vor, es ist früh am Morgen. Sie gießen sich Ihren ersten Kaffee des Tages ein. Der dampfende Becher in Ihrer Hand, das Gehäuse der Kaffeemaschine auf der Arbeitsplatte – all diese Alltagsgegenstände sind so selbstverständlich da. Auf dem Weg zur Arbeit drehen Sie den Zündschlüssel Ihres Autos um; das Armaturenbrett, die Kunststoffverkleidungen, ja selbst der Schlüssel selbst, wurden mit höchster Präzision gefertigt. Vielleicht greifen Sie später zum Smartphone – das schlanke Kunststoffgehäuse, die passgenauen Kopfhörer, das Gehäuse Ihres Laptops. Haben Sie sich jemals gefragt, wie all diese Dinge entstehen? Hinter jedem dieser Produkte steckt die Arbeit von Spezialisten, die man selten zu Gesicht bekommt: Werkzeugmacher und Formenbauer.
Ihre Werke – die Formen, Werkzeuge und Matrizen – sind die Schablonen, durch die unsere Alltagsgegenstände überhaupt erst Gestalt annehmen. Sie sind die unsichtbaren Helden hinter der Bühne der Fertigung, und ohne sie würde unsere moderne Welt ganz anders aussehen.
In diesem Blogartikel nehmen wir Sie mit auf eine Reise hinter die Kulissen des Werkzeug- und Formenbaus. Wir erzählen die Geschichte einer Branche, die für unseren Alltag unverzichtbar ist und doch oft im Verborgenen bleibt. Sie erfahren, warum Werkzeug- und Formenbau so bedeutend für Industrie und Gesellschaft ist, wie er sich historisch entwickelt hat und warum gerade Deutschland in diesem Bereich eine Führungsrolle innehat. Wir werfen einen praxisnahen Blick in Werkstätten, wo Funken fliegen und Präzision auf Handwerkskunst trifft, und schauen auf die Herausforderungen und Zukunftsperspektiven dieser Hightech-Branche. Begleiten Sie uns durch die Welt der Formen und Werkzeuge – einer Welt voller spannender Geschichten, Fakten und Menschen mit Leidenschaft für Perfektion. Und lernen Sie, warum PolyTALENT diese Branche so gut kennt, dass sie zum verlässlichen Kompass in diesem oft komplexen Terrain geworden sind.
Die Bedeutung des Werkzeugbaus für Alltag und Industrie
Wir alle nutzen täglich zahllose Produkte, ohne darüber nachzudenken, wie sie entstehen. Werkzeug- und Formenbau ist die stille Kunst, die hinter fast jedem industriell hergestellten Gegenstand steht. Vereinfacht gesagt: Werkzeugmacher und Formenbauer fertigen die Gussformen, Presswerkzeuge und Vorrichtungen, mit denen Materialien in Form gebracht werden. Ob eine Plastikflasche, ein Autotür-Panel aus Blech oder die Glasflasche für Ihren Lieblingssaft – sie alle verdanken ihre Form einem Werkzeug oder einer Form, die zuvor jemand entworfen und gebaut hat. Die meisten Gegenstände des täglichen Bedarfs könnten ohne diese Formen nicht in Serie produziert werden. Man könnte sagen, Werkzeuge und Formen bringen die Serienprodukte unseres täglichen Lebens in Form.
Dabei reicht die Bedeutung weit über Haushaltsgegenstände hinaus. Ganze Branchen hängen vom Werkzeug- und Formenbau ab: Automobilhersteller benötigen riesige Stahlpresswerkzeuge, um Karosserieteile zu stanzen; Medizintechnik-Firmen verlassen sich auf filigrane Formen für präzise Kunststoffteile von Spritzen oder Prothesen; in der Verpackungsindustrie entstehen Joghurtbecher, Flaschenverschlüsse und Lebensmittelverpackungen erst durch ausgeklügelte Spritzgussformen. Elektronik-Geräte – vom Küchenmixer bis zum Smartphone – verdanken ihre passgenauen Gehäuse ebenfalls diesem Handwerk. Ohne Werkzeugbau gäbe es keine massenhafte Produktion in der hohen Qualität und Präzision, die wir heute erwarten. Einfache Beispiel: Der berühmte dänische Spielzeughersteller Lego könnte seine bunten Steine nicht millionenfach so maßhaltig produzieren, würden nicht extrem präzise Spritzgussformen zum Einsatz kommen. Solche Formen erlauben Toleranzen bis in den Hundertstel-Millimeter-Bereich – so passt jedes Steinchen perfekt auf das nächste. Jede dieser Formwerkzeuge ist ein kleines Meisterwerk für sich und oft extrem langlebig: Hochwertige Stahlformen können, richtig gewartet, Hunderttausende bis Millionen Stück produzieren, ohne an Genauigkeit einzubüßen.
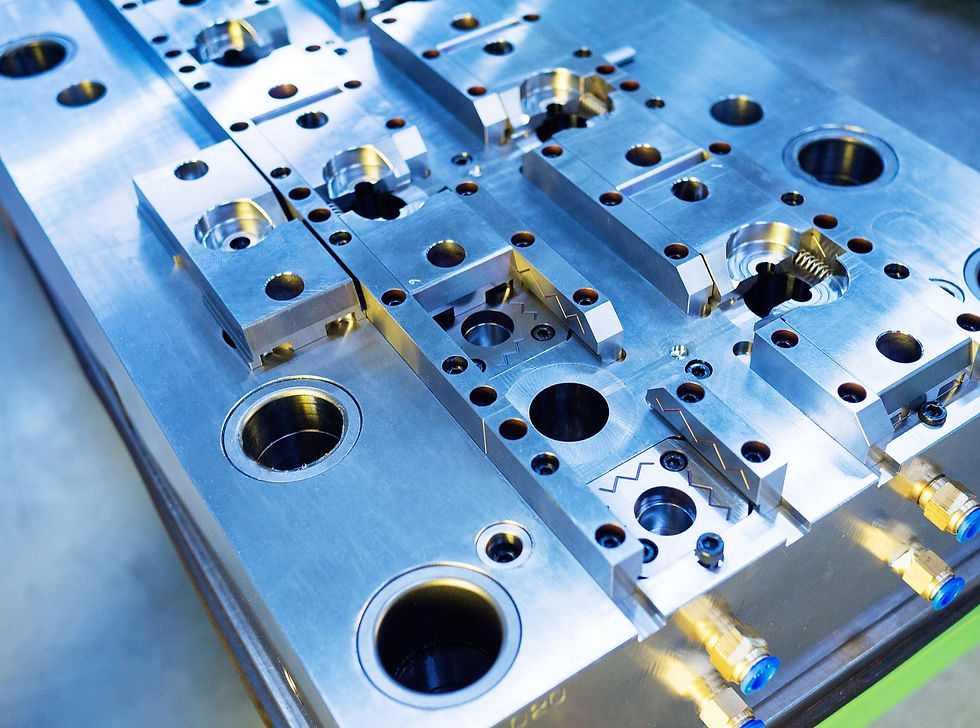
Ein faszinierender Aspekt ist, dass all diese Formen und Werkzeuge selbst Unikate sind. Anders als die Massenprodukte, die sie herstellen helfen, wird jede Form individuell für ein bestimmtes Bauteil angefertigt. Kein Werkzeug gleicht dem anderen – jede Form ist eine Sonderanfertigung, ein Einzelstück, geschaffen für die effiziente Serienfertigung von genau jenem einen Teil. Damit sind Werkzeugmacher wahre Ermöglicher: Ihre Unikate bilden die Grundlage dafür, dass millionenfache Kopien eines Produkts entstehen können. Sie arbeiten mit höchster Präzision, oft im Bereich weniger tausendstel Millimeter, denn nur so kann sichergestellt werden, dass später jedes produzierte Teil passt und funktioniert. Dieses extreme Qualitätsbewusstsein spiegelt sich auch in den Kosten und in der Komplexität der Werkzeuge wider. Die Herstellung einer Form oder eines Werkzeugs erfordert enorme Investitionen – sowohl finanziell als auch in puncto Zeit und Know-how. Ein einzelnes Spritzgusswerkzeug kann je nach Größe und Komplexität mehrere zehntausend bis hunderttausende Euros kosten. So viel steckt hinter einem scheinbar simplen Alltagsgegenstand, bevor er überhaupt auf den Markt kommt. Zum Vergleich: Eine Form für einen simplen Spielzeugbaustein kann leicht über 100.000 US-Dollar kosten – doch sie hält dann auch jahrelang und produziert hunderttausende identischer Teile. Das zeigt, welch unsichtbare Wertschöpfung in unserem Alltag verborgen ist.
Kurzum: Werkzeug- und Formenbau ist die Schlüsseltechnologie im Hintergrund unserer modernen Welt. Er verbindet Ingenieurskunst mit Handwerk und ermöglicht den Spagat zwischen Kreativität im Design und Effizienz in der Produktion. Jedes Auto, jedes Haushaltsgerät, jedes Smartphone erzählt indirekt auch die Geschichte der Formenbauer, die ihm seine Form gegeben haben. Die Leistung dieser Fachleute bleibt meist unsichtbar, doch sie bildet das Fundament, auf dem Industrie und Konsumgüterproduktion aufbauen. Es lohnt sich also, einen genaueren Blick auf diese stille, präzise Kunst zu werfen – von ihren Anfängen bis zu ihrem heutigen Hightech-Stand.
Historischer Abriss: Von den Anfängen bis heute
Der Werkzeug- und Formenbau mag heute hochtechnologisch sein, doch seine Wurzeln reichen weit zurück. Schon lange bevor es Kunststoff-Spritzguss gab, nutzten Menschen Formen, um Materialien in Form zu bringen. Man denke an die ersten Gussformen in der Metallverarbeitung: Bereits in vorindustrieller Zeit gossen Handwerker flüssiges Metall in Sand- oder Metallformen, um Waffen, Schmuck oder Geräte herzustellen. Auch in der Glasherstellung des 18. und 19. Jahrhunderts kamen Formen zum Einsatz, um etwa Flaschen identisch herzustellen – ein früher Schritt in Richtung industrieller Reproduzierbarkeit. Doch als eigenständige Branche entstand der Werkzeug- und Formenbau erst richtig mit der Industrialisierung im 19. Jahrhundert. In dieser Ära wurden erstmals Maschinen entwickelt, mit denen man präzise Formen und Matrizen fertigen konnte, um die aufkommende Massenproduktion zu ermöglichen. Produkte aus Metall und Glas konnten dank neuer Gussformen effizienter und in größerer Stückzahl gefertigt werden. Es war die Zeit, in der auch im Maschinenbau die Idee von standardisierten Teilen aufkam – und dafür brauchte man natürlich präzise Werkzeuge, um identische Teile herstellen zu können.
Einen gewaltigen Schub erhielt der Formenbau durch die Erfindung und Verbreitung von Kunststoffen. In der zweiten Hälfte des 19. Jahrhunderts wurden die ersten künstlichen formbaren Materialien erfunden. Ein Meilenstein war die Entwicklung von Celluloid – einem der ersten Thermoplaste – durch Alexander Parkes und später John Wesley Hyatt. Hyatt experimentierte mit Celluloid als Ersatz für Elfenbein und entwickelte um 1868 eine Methode, daraus Billiardkugeln herzustellen. Dieses Unterfangen führte zur Konstruktion der ersten Spritzgießmaschine: 1872 erhielten John Wesley Hyatt und sein Bruder Isaiah ein Patent auf eine Maschine, die erwärmtes Celluloid in eine Form einspritzen konnte. Diese Erfindung markiert die Geburtsstunde des Kunststoff-Spritzgusses – und damit auch den Beginn des modernen Formenbaus für Kunststoffe. Erstmals war es möglich, komplexe Formen relativ schnell und wiederholgenau aus einem neuen Werkstoff zu fertigen. Zwar waren die ersten Anwendungen noch einfach (Kämme, Knöpfe und besagte Billiardkugeln), doch das Konzept war revolutionär: Man konnte nun nahezu jede beliebige Form kreieren, solange man eine passende Form besaß, in die man das Material presste.
Der nächste große Sprung kam im frühen 20. Jahrhundert. 1907 erfand Leo Hendrik Baekeland den Kunststoff Bakelit, den ersten vollsynthetischen Kunststoff überhaupt. Bakelit war ein duroplastischer Werkstoff, ideal für Elektroteile und Alltagsgegenstände, und er musste in Form gepresst werden, solange er heiß war. Der Siegeszug von Bakelit und anderen Kunststoffen machte den Formenbau endgültig zu einer gefragten Disziplin: Nun galt es, robuste Formen zu bauen, die dem hohen Druck und der Hitze standhielten, um diese neuen Materialien zu verarbeiten. In den 1920er und 1930er Jahren wurden Spritzgießmaschinen immer ausgereifter und die Formen immer komplexer. Die Hersteller experimentierten mit neuen Konstruktionen – z.B. der Zwei-Stufen-Plunger-Maschine, die präziser arbeitete – und die Formenbauer lernten, auch komplizierte Hohlräume und feine Details in Stahl oder anderen Formwerkstoffen umzusetzen.
Ein entscheidender Beschleuniger der Entwicklung war der Zweite Weltkrieg. In Kriegszeiten stieg der Bedarf an schneller, massenhafter Produktion sprunghaft an – auch bei Kunststoffteilen, da Metalle knapp und teuer waren. Injection Molding, wie die Amerikaner sagen, wurde in den 1940ern verbessert und verfeinert, um z.B. Gehäuse für Geräte, Schutzhelme, Fahrzeugkomponenten und andere Ausrüstungen effizient herzustellen. Historiker der Industrie bezeichnen den Zweiten Weltkrieg daher als Katalysator für Innovationen im Spritzguss. Die Prozesse wurden schneller, die Maschinen leistungsfähiger und zuverlässiger. Nach dem Krieg, in den 1950er und 1960er Jahren, erlebte die Plastikindustrie einen Boom: Überall wurden nun Konsumgüter aus Kunststoff nachgefragt – von Tupperdosen bis Spielzeug, von Fernsehergehäusen bis Autoteilen. Der Werkzeug- und Formenbau musste Schritt halten, und tat es auch: Die Formen wurden in dieser Zeit immer ausgefeilter, um Massenprodukte in nie dagewesener Vielfalt herzustellen.
Die zweite Hälfte des 20. Jahrhunderts war geprägt von rasanten technologischen Fortschritten in der Fertigungstechnik, die auch den Werkzeugbau revolutionierten. In den 1970er Jahren hielt die Numerische Steuerung (NC) Einzug in die Werkstätten, bald gefolgt von CNC-Maschinen (Computerized Numerical Control). Wo zuvor ein Formenbauer viele Stunden mit Handfräsen, Feilen und manuellem Bohren verbringen musste, konnten nun Werkzeugmaschinen gesteuert von Lochstreifen oder Computern komplexe Geometrien quasi „wie von Geisterhand“ aus dem Metallblock herausarbeiten. Das digital gesteuerte Fräsen und Drehen machte die Fertigung schneller und präziser. In den 1980ern kam dann die CAD-Software (Computer Aided Design) hinzu. Plötzlich ließen sich Formen am Computer dreidimensional entwerfen, visualisieren und bis ins Detail planen, bevor der erste Span überhaupt fiel. Simulationsprogramme konnten bereits im Voraus berechnen, wie z.B. der Kunststoff in der Form fließen würde, wo Luftblasen entstehen könnten oder ob sich das Teil beim Abkühlen verziehen würde – all das, bevor man teures Material investierte. Diese Virtualisierung hat die Entwicklungszeiten enorm verkürzt und die Erfolgsquote beim ersten Prototyp gesteigert.
Während CNC und CAD dem Werkzeugbau mehr Präzision und Geschwindigkeit brachten, rückte seit den 2000er-Jahren ein weiteres Technologiefeld ins Rampenlicht: die Additive Fertigung, insbesondere der 3D-Druck. Was zunächst nur für schnelle Prototypen gedacht war, entwickelt sich zu einer echten Ergänzung. Heute können Formenbauer mit 3D-Druckern beispielsweise hochkomplexe Geometrien erstellen, die mit klassischer Fräse nur schwer oder in Einzelteilen machbar wären. Etwa Einsätze mit optimierten Kühlkanälen im Inneren, die mithilfe generativer Verfahren hergestellt und dann in Stahlformen eingebettet werden. Dadurch kühlen die Spritzgussteile schneller ab, was die Zykluszeit und damit die Produktionskosten senkt – ein Beispiel für Innovation durch neue Technologien. Auch kleine Stückzahlen von Ersatzteilen oder Versuchswerkzeugen lassen sich heute dank 3D-Druck in Kunststoff oder Metall realisieren, ohne gleich einen wochenlangen Werkzeugbauprozess anzustoßen.
In jüngster Zeit wachsen außerdem die Themen Digitalisierung und Vernetzung immer stärker mit dem klassischen Handwerk des Werkzeugbaus zusammen. Man spricht vom „Werkzeugbau 4.0“, angelehnt an die Industrie-4.0-Idee. Maschinen in modernen Werkzeugbau-Betrieben sind untereinander vernetzt, tauschen Fertigungsdaten aus und optimieren Abläufe. Zukünftig könnten sogar intelligente Formen entstehen, die sich während des Produktionsprozesses selbst überwachen und anpassen. Forschungsprojekte in Deutschland arbeiten bereits an selbstjustierenden Werkzeugen, die etwa während der ersten Testläufe (Tryout) automatisch erkennen, wo es klemmt, und die Einstellungen feinjustieren, um zeitaufwändige manuelle Nacharbeit zu reduzieren. Solche Visionen zeigen: Der Werkzeug- und Formenbau ist keineswegs ein verstaubtes Gewerbe, sondern eine technikgetriebene Branche, die immer wieder neue Wendepunkte erlebt – von den Gussformen der frühen Industrialisierung über die Erfindung des Spritzgusses bis hin zur digitalen Revolution von heute. Jede dieser Phasen hat den Werkzeugbau geprägt und ihn noch wichtiger für unsere Wirtschaft gemacht.
Ein Blick zurück verdeutlicht somit eindrucksvoll, wie aus der anfänglichen, simplen Idee – „Wir brauchen eine Form, um ein Produkt zu fertigen“ – eine hoch spezialisierte Disziplin wurde. Werkzeug- und Formenbauer von heute treten in die Fußstapfen früherer Tüftler und Ingenieure, doch ihr Arbeitsumfeld hat sich dramatisch gewandelt. Was gleich geblieben ist: Ohne sie läuft nichts. Damals wie heute ermöglichen sie es, Visionen in greifbare Produkte umzusetzen – sei es die erste Kunststoffkamm aus den 1870ern oder das neueste E-Auto aus dem Jahr 2025.

Warum Werkzeugbau in Deutschland so wichtig ist
Deutschland und präziser Maschinenbau – das gehört historisch zusammen. Neben Automobilen und Maschinen ist auch der deutsche Werkzeug- und Formenbau weltweit zum Begriff geworden. Tatsächlich zählt Deutschland heute zu den führenden Standorten der Welt in dieser Branche. Das liegt an mehreren Faktoren, die in Kombination nahezu einzigartig sind. Zum einen verfügt Deutschland über eine lange Tradition und Erfahrung im Werkzeugbau. Viele Unternehmen blicken auf Jahrzehnte, manche über ein Jahrhundert Firmengeschichte zurück, in der das Know-how von Generation zu Generation weitergegeben wurde. Diese Tradition geht Hand in Hand mit einer Kultur der Präzision: Schon im Ausbildungssystem (Stichwort: duale Ausbildung zum Werkzeugmechaniker) wird größter Wert auf Genauigkeit und Gründlichkeit gelegt. Die daraus hervorgehenden hochqualifizierten Fachkräfte sind das Fundament des Erfolges. „Verlässlichkeit, Kreativität, lösungsorientiertes Arbeiten, Präzision und große Neugier – das sind unsere Stärken“. Und tatsächlich genießt das „German Engineering“ in diesem Sektor international einen exzellenten Ruf.
Ein weiterer Erfolgsfaktor ist die enge Verzahnung von Industrie und Forschung. In kaum einem Land arbeiten Unternehmen so eng mit technischen Universitäten und Instituten zusammen wie hier. Es gibt spezialisierte Forschungsstellen – etwa das Kunststoff-Institut Lüdenscheid oder Fraunhofer-Institute – die gemeinsam mit mittelständischen Werkzeugbauern neue Materialien, bessere Kühlmethoden oder digitalisierte Prozessketten entwickeln. Dieser Technologietransfer hält die Branche innovativ und wettbewerbsfähig. Zugleich existiert ein starkes Netzwerk und Austausch: Verbände wie der VDWF fördern den Wissenstransfer zwischen Betrieben, organisieren Workshops, Messen (z.B. die Moulding Expo in Stuttgart) und gemeinsame Projekte. Solche Kooperationen sind besonders für kleine und mittlere Betriebe wichtig, um auf dem neuesten Stand zu bleiben.
Deutschland ist in diesem Bereich vor allem für Premium-Werkzeuge bekannt. Während global gesehen Länder wie China in den letzten Jahrzehnten große Marktanteile mit günstigeren Standardwerkzeugen erobert haben, konzentrieren sich viele deutsche Werkzeugbauer auf hochkomplexe, anspruchsvolle Projekte – etwa Formen für sicherheitsrelevante Bauteile in Autos, hochpräzise Mehrkomponenten-Spritzgussformen für Medizinprodukte oder langlebige Druckgussformen für die Luftfahrt. Hier zählt Qualität und Zuverlässigkeit mehr als der billigste Preis. „Der deutsche Werkzeugbau wird zu Recht weltweit als führend für Premiumwerkzeuge geschätzt“, schreibt die Fachzeitschrift Der Stahlformenbauer im Januar 2025. In einem kleinen fränkischen Dorf namens Rügland etwa sitzt ein Formenbau-Unternehmen, das für seine hochpräzisen Spritzgusswerkzeuge international bekannt ist. Solche Hidden Champions – oft familiengeführt und in ländlichen Regionen beheimatet – begründen den Ruf der deutschen Branche. Es sind Firmen mit vielleicht 50 oder 100 Mitarbeitern, die jedoch für die größten Konzerne der Welt arbeiten und deren Produkte überall im Einsatz sind. Man findet sie in ganz Deutschland: traditionell viele in Baden-Württemberg und Bayern (im Umfeld der Automobil- und Maschinenbauindustrie), aber auch in Regionen wie Südwestfalen oder Ostdeutschland gibt es Cluster von Werkzeugbauern mit langer Tradition.
Diese Stellung als „Werkbank der Welt“ im Formenbau ist nicht nur ein Prestige. Sie hat handfeste wirtschaftliche Bedeutung: Die Branche erwirtschaftet Milliardenumsätze und beschäftigt zehntausende Fachkräfte im Land. Darüber hinaus sichert ein starker lokaler Werkzeugbau die Wettbewerbsfähigkeit anderer Industriezweige. Warum? Weil gerade bei Neuentwicklungen eine enge Abstimmung zwischen Produktentwicklung und Werkzeugbau goldwert ist. Wenn der Automobilbauer für ein neues Modell schnell Änderungen benötigt, ist es ideal, wenn der Formenbauer nicht am anderen Ende der Welt sitzt. Die Nähe erleichtert Kommunikation, verkürzt Transportwege und Reaktionszeiten. Viele deutsche Hersteller haben die Erfahrung gemacht, dass die scheinbare Kostenersparnis durch Billigwerkzeuge aus dem Ausland oft durch Qualitätsprobleme oder fehlende Flexibilität zunichte gemacht wird. Deshalb heißt es in sensiblen Bereichen häufig: Lieber ein Werkzeug "Made in Germany".
Allerdings ruht sich die Branche nicht auf Lorbeeren aus – sie muss es auch gar nicht, denn sie steht beständig unter Druck, sich zu beweisen. In den letzten Jahren spüren auch deutsche Werkzeug- und Formenbauer verstärkt Gegenwind in Form von Herausforderungen, die ihre wichtige Position bedrohen könnten. Dazu zählen wir im nächsten Abschnitt die größten Stolpersteine und wie die Branche gewillt ist, sie zu meistern, um auch künftig eine tragende Rolle zu spielen.
Ein Blick in die Praxis: Wie Formen & Werkzeuge entstehen
Um zu verstehen, was Werkzeugbau wirklich bedeutet, lohnt sich ein praktischer Blick in eine typische Werkzeugmacher-Werkstatt. Stellen wir uns einen erfahrenen Formenbauer vor – nennen wir ihn Markus. Markus arbeitet in einem mittelständischen Betrieb im Schwarzwald, der auf Spritzgussformen spezialisiert ist. Heute steht er vor einer spannenden Aufgabe: Ein großer Automobilzulieferer hat den Auftrag für die Form eines neuen Scheinwerfergehäuses erteilt. Vom CAD-Modell bis zur fertigen Form und den ersten Testteilen liegt nun ein weiter Weg vor Markus und seinem Team.
Schritt 1: Die Planung und das Design. Alles beginnt am Computer. Die Kundenkonstrukteure haben das 3D-Modell des Scheinwerfergehäuses geliefert. Markus und seine Kollegen – spezialisierte Werkzeugkonstrukteure – laden das Modell in ihre CAD-Software. Jetzt wird die Form entworfen, die später dieses Gehäuse produzieren soll. Dabei müssen sie viele Fragen beantworten: Aus wie vielen Teilen soll das Werkzeug bestehen (meist gibt es zwei Hälften, manchmal aber auch komplizierte Schieber und Einsätze)? Wo platziert man die Angussstelle, also die Öffnung, durch die der Kunststoff ins Werkzeug fließt? Wie gestaltet man die Kühlkanäle im Werkzeug, damit das Teil möglichst gleichmäßig und schnell abkühlt? Jede Rippe und jede Bohrung im Bauteil findet ihr Spiegelbild in einem Steg oder Zapfen im Werkzeug. Mit spezieller Software wird eine Formfüllsimulation durchgeführt: virtuell schießen die Ingenieure flüssiges Plastik in ihr virtuelles Werkzeug und beobachten am Bildschirm, ob alles glatt geht – ob sich irgendwo Luftblasen fangen oder ob dünne Stellen problematisch sind. Nach einigen Iterationen steht das virtuelle Design der Form fest.
Schritt 2: Vom virtuellen Modell zum echten Stahl. Jetzt wird es laut in der Werkstatt. Ein großer Stahlblock wurde bereits angeliefert – hochwertiger Werkzeugstahl, der gehärtet und bereit ist, zum Präzisionswerkzeug zu werden. Markus ruft das NC-Programm auf, das er aus dem CAD-Modell erstellt hat. Eine CNC-Fräsmaschine wird vorbereitet: Sie ist mannshoch, mit Gehäuse und Kühlmittelanlage, und hat ein Magazin voller verschiedener Fräsköpfe. Mit einem Druck auf den Knopf beginnt der Fräskopf zu surren und sich in den Stahlblock zu graben. Über Stunden (manchmal Tage) hinweg fräst die Maschine Kavität um Kavität in den Stahl – erst grob, dann immer feiner. Späne fliegen, Kühlflüssigkeit spritzt. Die Werkstatt klingt wie ein orchestriertes Dröhnen und Kreischen von Metall. Immer wieder überprüft Markus das Ergebnis mit kritischem Auge und präzisen Messmitteln. Koordinatenmessgeräte kommen zum Einsatz, um die Maße auf wenige Hundertstel Millimeter zu prüfen. Parallel dazu läuft vielleicht eine zweite Maschine: Für besonders feine Konturen oder tiefe, schmale Formen nutzt man das Erodieren (EDM). Dabei senkt sich eine Elektrode in Form der gewünschten Kontur in den Stahl und funkenerodiert Material ab – ein Prozess, der zwar langsamer als Fräsen ist, aber unverzichtbar, wenn es um feinste Ecken und Kanten geht (etwa bei einem Formeinsatz für das Firmenlogo im Scheinwerferglas).
Die Werkstatt von Markus verbindet modernste Maschinen mit bewährtem Handwerk. Während an einer Ecke die CNC-Maschine selbsttätig fräst, sitzt in einer anderen Ecke ein Kollege mit geübter Hand und schleift einen Formeinsatz nach. Funken sprühen, wenn er mit dem Schleifbock eine Kante exakt abrundet – hier kommt es auf das Fingerspitzengefühl an. Sobald die maschinelle Bearbeitung abgeschlossen ist, wird das Werkzeug von Hand feinbearbeitet. Es geht ans Polieren der Kavitäten, damit später die Kunststoffteile glänzen und sich leicht aus der Form lösen. Oft müssen Formen spiegelglatt poliert werden, insbesondere wenn das spätere Bauteil eine glänzende Oberfläche haben soll (man denke an einen Chrom-zum-Look-Kühlergrill oder die Oberfläche eines Smartphone-Displayschutzes). Diese Arbeit erfordert enorme Geduld: In manchen Fällen sitzt der Polierer mit feinstem Schleifpapier und Polierpaste stunden- oder tagelang an einem einzigen Formeinsatz, bis jede Rille entfernt ist. „Das ist klassische Handwerkskunst“, würde Markus sagen – hier zeigt sich, dass trotz aller Computer der Mensch als Meister seines Fachs unersetzlich ist.
Schritt 3: Montage und Probelauf. Nachdem alle Einzelteile der Form gefertigt und bearbeitet sind, wird das Werkzeug montiert. Werkzeugbauer sprechen oft vom „Werkzeug“ auch dann, wenn es aus vielen Komponenten besteht: Grundplatten, Formeinsätze, Auswerfer (kleine Stifte, die später das fertige Teil aus der Form drücken), eventuelle Schieber oder Kernzüge, die Hinterschnitte entformen helfen, Kühlleitungen, Heizpatronen – alles muss am richtigen Platz sitzen. Ziehöl wird aufgetragen, Schrauben werden mit dem Drehmomentschlüssel angezogen. Dann ist es soweit: Die Form wird zum ersten Mal in eine Spritzgießmaschine eingebaut für den Tryout, den Probelauf. Alle sind gespannt: Funktioniert die Konstruktion wie geplant?
Die Spritzgießmaschine schließt mit einem satten Klonk, und die hydraulische Presse hält die Form mit mehreren hundert Tonnen Schließkraft zusammen (große Maschinen können über 1000 Tonnen Druck ausüben – umgerechnet das Gewicht von mehr als fünf voll beladenen Jumbo-Jets!). Flüssiger, 250°C heißer Kunststoff wird eingespritzt. Sekunden vergehen, dann öffnet sich die Form – und heraus fällt: ein Scheinwerfergehäuse, noch warm und mit einem Angussrest dran. Markus nimmt es in die Hand. Er und seine Kollegen prüfen das erste Teil mit geübtem Blick. Sitzen alle Clips und Haken richtig? Ist das Material bis in die letzte Ecke geflossen oder gibt es Lunker (kleine Fehlstellen)? Wie passt das Teil zum restlichen Scheinwerfermodul? Jetzt zeigt sich, wie gut Design und Fertigung waren. Oft sind bei ersten Musterungen kleine Anpassungen nötig: Hier vielleicht die Temperatur etwas erhöhen, dort die Kühlung leicht drosseln, damit keine Einfallstelle entsteht. Feinabstimmung nennt man das – ein Schritt, der viel Erfahrung erfordert. Sollte ein Formeinsatz doch noch optimiert werden müssen, geht es zurück an die Werkbank: Ein winziger Bereich wird nachgefräst oder per Hand nachgearbeitet.
Nach ein, zwei Optimierungsrunden ist es geschafft: Die Form produziert fehlerfreie Teile innerhalb der Toleranzen. Was für ein Moment! Für Außenstehende mag es „nur“ ein weiteres Autoteil sein, für Markus und sein Team ist es das greifbare Resultat harter Arbeit. Wochen, teils Monate, nachdem die CAD-Planung begann, verlässt nun ein perfektes Werkzeug die Werkstatt – bereit, in der Fabrik des Kunden tausendfach im Einsatz zu sein. Und dieses Scheinwerfergehäuse? Dank Markus’ Form wird es nun im Automobilwerk in Serie gehen und in Tausenden Autos für Licht sorgen.
Diese Reise durch den Entstehungsprozess zeigt eindrücklich, wie anspruchsvoll und vielschichtig der Werkzeugbau ist. Es ist ein Zusammenspiel aus Hightech-Maschinen und menschlichem Know-how. Jeder Tag in so einer Werkstatt kann Überraschungen bringen: Mal bricht ein Fräser und man muss improvisieren; mal merkt man, dass eine Kundenzeichnung einen Fehler hat und man gemeinsam nach einer Lösung suchen muss. Formenbauer sind deshalb auch immer Problemlöser. Sie müssen einerseits das technische Verständnis für CAD, CNC und Werkstoffe haben, andererseits Kreativität und handwerkliches Geschick mitbringen, wenn es darum geht, ungewöhnliche Herausforderungen zu meistern. Kein Wunder, dass viele von ihnen ihren Beruf mit Stolz ausüben – sie wissen, dass ohne ihre Arbeit viele Ideen nicht in die Tat umgesetzt werden könnten.
Und noch etwas wird deutlich: Werkzeugbau ist Teamarbeit. Von den Konstrukteuren am Computer über die Maschinenbediener und Handwerker bis zu den Qualitätsexperten – sie alle tragen dazu bei, dass am Ende ein hervorragendes Werkzeug entsteht. Diese Zusammenarbeit, oft über viele Jahre eingespielt, ist Teil der besonderen Kultur in Werkzeugbaubetrieben. Nicht selten arbeiten hier mehrere Generationen, und Wissen wird direkt am Werkstück weitergegeben. Wer neu dazukommt, staunt vielleicht am Anfang, wie viel Detailwissen ein „alter Hase“ hat – über das Verhalten eines bestimmten Stahls beim Härten, über die beste Poliertechnik für eine bestimmte Oberfläche, oder über die Tücken einer bestimmten Spritzgussgeometrie. Dieses Erfahrungswissen macht den Wert der unsichtbaren Helden aus: Sie können auf Dinge achten, die ein Computer (noch) nicht bedenkt, und so dafür sorgen, dass die Produktion später reibungslos läuft.
Wenn Sie also das nächste Mal ein perfekt sitzendes Kunststoffteil in der Hand halten oder bewundern, wie die Teile Ihres neuen Geräts nahtlos zusammenpassen, denken Sie vielleicht einen Moment an diese Entstehungsgeschichte. Hinter jedem solchen Produkt steckt ein Team wie das von Markus, das oft monatelang getüftelt, geschliffen, gemessen und verbessert hat – damit Sie am Ende ein zuverlässiges, schönes und funktionales Produkt nutzen können.
Herausforderungen und Zukunftsaussichten der Branche
Trotz aller Erfolge und Hightech-Prozesse: Der Werkzeug- und Formenbau steht vor erheblichen Herausforderungen, besonders in Deutschland. Viele dieser Themen betreffen die gesamte Industrie, manche treffen Werkzeugbaubetriebe aber in besonderer Weise. Hier sind einige der drängendsten Punkte – und ein Blick darauf, wie die Branche damit umgeht und welche Chancen in der Zukunft liegen:
1. Fachkräftemangel und Generationenwechsel: Ein Problem, das man in nahezu jeder Werkstatt hört, ist die Sorge um Nachwuchs. Die alten Meister gehen nach und nach in Rente, doch es wird immer schwieriger, junge Menschen für diesen Beruf zu begeistern. Der Werkzeugmacher von heute muss hochqualifiziert sein – er vereint die Rollen eines Präzisionsmechanikers, CNC-Technikers, manchmal auch Programmierers. Doch vielen Jugendlichen ist gar nicht klar, welch spannende Tätigkeit sich dahinter verbirgt. Das Image der Industrieberufe hat gelitten, obwohl die Technik längst modern ist. Verbände wie der VDWF versuchen gegenzusteuern: Sie produzieren Imagefilme, gehen in Schulen, kooperieren mit Hochschulen, um Generation Z zu erreichen. Die Devise lautet: zeigen, wie innovativ und vielseitig der Werkzeugbau ist, und dass man hier mit Hightech arbeitet – nicht nur „an der Werkbank schwitzt“. Doch der Wettbewerb um kluge Köpfe ist hart, zumal Branchen wie IT oder Elektrotechnik locken. Für die meisten Betriebe ist klar: Sie müssen jungen Leuten attraktive Angebote machen, sei es mit Ausbildungskooperationen, Weiterbildung oder neuen Arbeitsmodellen, um Talente zu halten und zu fördern. Die Zukunft des Werkzeugbaus hängt maßgeblich davon ab, ob es gelingt, eine neue Generation von Experten auszubilden, die das Know-how übernehmen. Einige Betriebe experimentieren mit New Work Konzepten, flexiblen Arbeitszeiten oder der Beteiligung junger Mitarbeiter an Forschungsprojekten, um das Berufsfeld attraktiver zu gestalten.
2. Globaler Kostendruck und Konkurrenz: Die Konkurrenz im Werkzeugbau ist längst global. Besonders aus China, aber auch aus anderen aufstrebenden Industrienationen, kommen Angebote für Formen und Werkzeuge, die preislich oft deutlich unter den hiesigen liegen. Viele Kunden – etwa in der Konsumgüterindustrie – haben in den vergangenen Jahren versucht, durch Importe aus Niedriglohnländern Kosten zu sparen. Das hat manchen deutschen Betrieben zugesetzt. Der Kostendruck steigt dadurch enorm. Deutsche Werkzeugbauer begegnen dem, indem sie ihren Vorsprung in Qualität und Technik ausbauen. Sie setzen auf höhere Automatisierung in der Fertigung, um effizienter zu werden (Stichwort: Lights-out Manufacturing, also Fertigung über Nacht ohne Personal durch Roboter und Automatisierung). Einige spezialisieren sich noch stärker – z.B. nur noch hochkomplexe Mehrkomponenten-Werkzeuge, die andere nicht liefern können. Andere kooperieren, um im Paket größere Aufträge zu stemmen. Und tatsächlich zeigt sich: Bei anspruchsvollen Projekten zählen für viele Kunden weiterhin Zuverlässigkeit, Präzision und Langlebigkeit mehr als nur der Preis. „Die Branche ist trotz ihrer Schlüsselposition in der Öffentlichkeit wenig bekannt“, heißt es treffend – aber das soll sich ändern. Durch verstärkte Öffentlichkeitsarbeit will man auch Auftraggebern den Wert guter Werkzeuge bewusster machen. Gleichzeitig gibt es Bemühungen, eine faire Wettbewerbsumgebung zu schaffen – etwa durch Eintreten für internationale Qualitätsstandards und gegen Produktpiraterie (denn es kam vor, dass Konstruktionsdaten gestohlen und billig kopiert wurden). Ein weiterer Trend: Mancher Betrieb orientiert sich international und gründet eigene Auslandsniederlassungen – z.B. in China – um vor Ort präsent zu sein, ohne das Heimat-Know-how komplett abwandern zu lassen.
3. Kürzere Produktlebenszyklen und Zeitdruck: In vielen Branchen müssen Produkte immer schneller auf den Markt kommen. Für den Werkzeugbau bedeutet das: Noch kürzere Durchlaufzeiten. Wo früher vielleicht 6-12 Monate für Entwicklung und Bau eines neuen Werkzeugs vorgesehen waren, sind es heute oft nur noch wenige Monate, manchmal Wochen. „Kürzere Lieferzeiten“ sind explizit eine der Herausforderungen, die Werkzeugbaubetriebe in Regionen wie Südwestfalen nennen. Das erfordert optimierte Prozesse, paralleles Arbeiten (z.B. schon Teile der Form fertigen, während andere noch konstruiert werden) und häufig einen Einsatz am Limit. Verzögerungen kann sich kaum jemand leisten, denn wenn das Werkzeug zu spät kommt, verzögert sich die ganze Produktmarkteinführung des Kunden. Hier spielt die Digitalisierung wiederum eine wichtige Rolle: Durch vernetzte Systeme und Simulationen kann viel Zeit eingespart werden. Beispielsweise ermöglichen virtuelle Probeläufe am Computer, die Anzahl realer Tryouts zu reduzieren. Zukünftig könnten intelligente Werkzeuge auch hier helfen, indem sie sich selbst justieren und schneller produktionsbereit sind. Dennoch bleibt Zeitdruck ein Faktor, der den Alltag vieler Werkzeugbauer bestimmt – und nur durch Effizienz und smarte Planung zu bewältigen ist.
4. Digitalisierung und Industrie 4.0: Viele Werkzeugbaubetriebe befinden sich mitten in der digitalen Transformation. Das heißt konkret: Sie investieren in neue Software, vernetzen ihre Maschinen, setzen auf Datenanalyse. Der Nutzen? Mehr Transparenz und bessere Entscheidungsgrundlagen. Wenn z.B. alle Maschinen in einer Fertigungshalle ihre Echtzeitdaten melden, kann der Fertigungsleiter sofort sehen, wo Engpässe entstehen, welches Teil als nächstes fertig wird oder wo ggf. ein Wartungsbedarf auftaucht. Moderne Systeme ermöglichen sogar eine vorausschauende Wartung: Sensoren im Werkzeug erkennen Verschleiß und melden, wenn z.B. ein Auswerferstift getauscht werden sollte, bevor er bricht. Das verhindert Ausfallzeiten. Allerdings ist die Umsetzung nicht trivial, gerade für kleinere Betriebe. Viele klagen, dass Insellösungen existieren, die noch nicht ausreichend vernetzt sind. Die Herausforderung besteht darin, die richtigen Investitionen zu tätigen, die sich auch lohnen – „nicht mit Kanonen auf Spatzen zu schießen“, wie ein Berater es formulierte. Ein gelungenes Beispiel ist das erwähnte Projekt "Werkzeugbau der Zukunft" in Südwestfalen, wo mehrere Firmen gemeinsam einen digitalen Datenraum betreiben. Dort teilen sie anonymisiert Produktionsdaten, um aus einer größeren Datenbasis Muster zu erkennen und Prozesse zu verbessern. Solche Kooperationen könnten Schule machen und gerade kleineren Unternehmen helfen, die digitale Klaviatur zu spielen. Im Ergebnis verspricht die Digitalisierung dem Werkzeugbau, noch effizienter und flexibler zu werden – unabdingbar, um im internationalen Vergleich vorn zu bleiben.
5. Nachhaltigkeit und neue Materialien: Wie alle Industrien muss sich auch der Werkzeugbau dem Thema Nachhaltigkeit stellen. Einerseits intern: Werkstätten und Maschinen verbrauchen Energie – steigende Energiekosten sind ein Thema, das auf den Margen lastet. Hier sind Effizienz und ggf. eigene Energiegewinnung (Solaranlagen auf den Hallendächern etc.) gefragt. Andererseits die Produkte: Neue Materialien wie biobasierte Kunststoffe oder Rezyklate (recycelte Kunststoffe) gewinnen an Bedeutung. Diese können andere Eigenschaften haben, etwa stärker abrasiv sein oder andere Schwindmaße haben. Die Formenbauer müssen ihr Wissen stetig erweitern, um auch für solche Materialien optimale Werkzeuge zu liefern. Nachhaltigkeit im Werkzeugbau heißt auch, Werkzeuge länger nutzbar zu machen, Reparaturfähigkeit einzuplanen und Rohstoffe zu sparen. Schon bei der Konstruktion überlegt man, wie man z.B. zerspanendes Material (Späne) minimiert oder ob bestimmte Teile der Form vielleicht 3D-gedruckt werden können, um Abfall zu reduzieren. Ein interessanter Aspekt: Ein hochwertiges Werkzeug an sich ist schon nachhaltig, denn es ermöglicht oft Millionen von Teilen zu produzieren. Je länger ein Werkzeug hält und je besser es produziert, desto geringer ist der Ressourcenverbrauch pro hergestelltem Teil. Und hierin sind deutsche Formenbauer gut: langlebige, robuste Werkzeuge zu bauen. Dennoch, Themen wie CO₂-Fußabdruck oder Einsatz von umweltfreundlicheren Kühl- und Schmiermitteln werden in Zukunft verstärkt eine Rolle spielen. Einige Umfragen zeigen, dass vielen Unternehmen im Werkzeugbau noch klare Nachhaltigkeitsstrategien fehlen – hier besteht also auch eine Herausforderung, aber ebenso eine Chance, sich als Vorreiter zu positionieren.
Trotz dieser Herausforderungen gibt es vielversprechende Zukunftsaussichten. Die Industrie zeigt sich äußerst anpassungsfähig. Sie hat in der Vergangenheit jede technische Revolution gemeistert – von Handarbeit zu CNC, von Zeichentisch zu CAD – und wird das auch weiterhin tun. Viele Unternehmen arbeiten bereits an der nächsten Generation von Werkzeugen: noch präziser, vielleicht mit integrierten Sensoren und Aktuatoren. Die Nachfrage nach qualitativ hochwertigen Werkzeugen wird bestehen bleiben, solange es Produktion gibt. Besonders zukunftsträchtige Felder sind etwa E-Mobilität (neue Bauteile für Elektroautos benötigen ebenfalls Formen und Werkzeuge, z.B. für Batteriekomponenten oder leichte Kunststoffstrukturen) und Medizintechnik (hier steigt der Bedarf an Spezialteilen rasant, und damit der Bedarf an präzisen Werkzeugen). Ein Geschäftsführer brachte es auf den Punkt: „Ohne uns steht die Fabrik. Unsere Branche ist klein, aber entscheidend.“ Die Leistung der Werkzeugmacher sichtbar zu machen und gleichzeitig immer einen Schritt voraus zu sein, darin liegt die Zukunft. Man darf gespannt sein, wie die unsichtbaren Helden weiter an ihrer Erfolgsgeschichte schreiben – und welche Innovationen sie als Nächstes aus dem Hut zaubern, damit die Produkte von morgen Realität werden.

PolyTALENTs tiefgehendes Verständnis für den Markt
Warum kennt PolyTALENT die Werkzeug- und Formenbau-Branche so gut? Ein Blick auf den Hintergrund des Unternehmens gibt Aufschluss. PolyTALENT ist kein branchenfremder Generalist, sondern wurde von Menschen aus der Kunststoff- und Werkzeugbaubranche gegründet. Der Gründer Mehmet Tarti etwa verbrachte über ein Jahrzehnt in der Kunststoffindustrie, baute sich dort ein breites Netzwerk auf und sammelte Erfahrungen in Prozessen, Vertrieb und Produkten. Diese praktische Branchenkenntnis bildet das Fundament von PolyTALENT. Man versteht bei PolyTALENT die spezifischen Herausforderungen und Anforderungen der Industrie aus erster Hand – sei es der schon erwähnte Fachkräftemangel, die rasanten technischen Entwicklungen oder die Besonderheiten einzelner Sektoren wie Spritzguss, Extrusion oder eben Werkzeugbau. Dieses Know-how fließt in die tägliche Arbeit ein: Als Spezialist für Personal und Recruiting in der Kunststoff-, Polymer- und Werkzeugbaubranche spricht PolyTALENT die Sprache der Industrie.
Was bedeutet das konkret? PolyTALENT weiß, worauf es ankommt, wenn Unternehmen in dieser Branche nach Verstärkung suchen. Ob ein Formenbau-Betrieb einen erfahrenen CNC-Fräser sucht, ob ein Kunststoffverarbeiter einen Projektleiter mit Werkzeugbauverständnis braucht oder ein Maschinenbauer einen Vertriebsingenieur für Werkzeugsysteme – PolyTALENT kann einschätzen, welche Qualifikationen wirklich wichtig sind und wo solche Fachkräfte zu finden sind. Durch das bestehende Netzwerk von über 10000 Kontakten in der Branche hat PolyTALENT einen direkten Draht zu vielen Experten und Entscheidern. Das Unternehmen verfolgt ständig die Marktbewegungen: Welche Technologien kommen, welche Firmen wachsen, wo tun sich Engpässe auf? Diese Marktbeobachtung ist Teil der Dienstleistung, aber auch Ausdruck echten Interesses an der Branche.
Als Branchenexperte fungiert PolyTALENT auch oft als Bindeglied und Übersetzer zwischen unterschiedlichen Welten. Zum Beispiel zwischen einem jungen IT-Spezialisten und einem traditionellen Werkzeugbau-Unternehmen: PolyTALENT versteht die Kultur und Bedürfnisse beider Seiten und kann so Missverständnisse vermeiden und gemeinsame Ziele betonen. Oder zwischen einem internationalen Kandidaten und einem deutschen Mittelständler: Das Team weiß, worauf es ankommt, damit jemand fachlich und menschlich in den Betrieb passt. Diese Treffsicherheit kommt nicht von ungefähr, sondern von der tiefen Vertrautheit mit den typischen Abläufen, Strukturen und auch Herausforderungen in Werkzeugbau und Kunststoffindustrie.
Zudem zeigt PolyTALENT, dass man Innovation in der eigenen Arbeitsweise mit Branchenwissen kombinieren kann. Als digitaler Headhunter setzt PolyTALENT moderne Tools und KI-Technologien ein, um die passenden Talente für Unternehmen aufzuspüren. Dennoch verliert man nie den direkten menschlichen Bezug, da man genau weiß, wie wichtig Vertrauen und fachliche Glaubwürdigkeit in dieser Community sind. Im Gespräch mit einem Kandidaten kann PolyTALENT beispielsweise auf Augenhöhe über Themen wie Spritzguss, CAD/CAM oder Prozessoptimierung reden – denn man kennt diese Begriffe nicht nur aus Stellenbeschreibungen, sondern aus der eigenen Erfahrung. So etwas schafft Vertrauen bei Fach- und Führungskräften, die schnell merken: Hier versteht mich jemand wirklich und will mir keine x-beliebige Stelle vermitteln, sondern genau die richtige in „meiner“ Branche.
PolyTALENTs tiefgehendes Marktverständnis zeigt sich letztlich daran, dass das Unternehmen seit seiner Gründung eine wachsende Zahl an Kunden aus dem Werkzeug- und Formenbau betreut. Zufriedene Werkzeugbau-Unternehmer bestätigen, dass PolyTALENT die Komplexität und Bedeutung ihrer Arbeit erkennt – und entsprechend engagiert ist, die richtigen Experten für sie zu finden. In einer Branche, in der oft gegenseitiges Verständnis fehlt (Personalvermittler verstehen die Technik nicht, und Techniker oft nicht die Personaler), nimmt PolyTALENT eine besondere Rolle ein: als Übersetzer, Unterstützer und Wegbereiter dafür, dass die unsichtbaren Helden von morgen die passenden Wirkungsstätten finden.
Ohne in plumpe Eigenwerbung zu verfallen, darf man sagen: PolyTALENT trägt mit seinem spezialisierten Ansatz selbst ein Stück dazu bei, dass die Werkzeugbaubranche gestärkt wird – indem es hilft, den entscheidenden Faktor Mensch am richtigen Platz zu positionieren. Denn alle Technik und Innovation nützt nichts, ohne fähige Hände und kluge Köpfe, die sie einsetzen. PolyTALENT weiß das und handelt danach. Genau dieses Verständnis – gepaart mit echter Begeisterung für Werkzeug- und Formenbau – macht PolyTALENT zum Branchenkenner, auf dessen Einschätzungen man bauen kann.
Fazit & abschließender Gedanke
Der Werkzeug- und Formenbau ist wahrlich eine Welt der unsichtbaren Helden. Tagtäglich sorgen sie dafür, dass millionenfach Produkte entstehen können, die unser Leben komfortabler, sicherer und schöner machen. Ohne die Arbeit von Werkzeugmachern und Formenbauern gäbe es keine hochwertigen, langlebigen Produkte in der Vielfalt und Präzision, die wir heute kennen. Sie sind die stillen Architekten hinter den Kulissen der Fertigung, die mit ihrem Können und ihrer Innovationskraft die Basis für zahllose Erzeugnisse schaffen. Ihr Beitrag bleibt für die meisten von uns unsichtbar – doch ohne sie wäre unsere moderne Welt kaum denkbar.
Wenn wir also das nächste Mal einen Alltagsgegenstand in Händen halten, lohnt es sich, einen Moment innezuhalten und den Weg dieses Produkts zurückzuverfolgen. Fast unweigerlich landet man bei einem Formwerkzeug und damit bei seinen Schöpfern. Vielleicht trinken Sie morgen Ihren Kaffee mit einem neuen Bewusstsein dafür, dass der Becher, der Deckel und sogar der Milchtütenverschluss deshalb existieren, weil es irgendwo hochpräzise gefertigte Formen gibt, die genau diese Teile ausformen. Der Werkzeugbau durchzieht, ohne großes Aufheben, unser gesamtes Wirtschaftsleben: von der Kleinserie einer Designerlampe bis zur Millionenauflage des nächsten Smartphone-Modells.
Deutschland hat in diesem Bereich Glück und Verantwortung zugleich – Glück, weil es so viele der besten Werkzeugbauer beherbergt, Verantwortung, weil wir dieses Erbe und Know-how in die Zukunft tragen müssen. Die Branche steht vor Herausforderungen, aber wie wir gesehen haben, gibt es auch viele Ideen und Initiativen, um diese zu meistern. Die unsichtbaren Helden arbeiten längst daran, noch besser, digitaler und nachhaltiger zu werden, ohne ihre Wurzeln der Präzision und Qualität zu vergessen.
Zum Schluss bleibt ein Aufruf zur Wertschätzung: Vielleicht kennt jeder von uns jemanden, der in diesem Bereich tätig ist – sei es der Nachbar, der „in der Firma Formen baut“, oder ein Familienmitglied, das als Ingenieur für Kunststofftechnik arbeitet. Machen wir uns bewusst, welch Expertise und Leidenschaft dahintersteckt. Und ermutigen wir junge Menschen, einen Blick in diese Branche zu werfen – denn dort kann man tatsächlich im wahrsten Sinne des Wortes Grundlagen für die Zukunft schaffen. Jede neue Technologie, jedes neue Produkt beginnt damit, dass jemand die passenden Werkzeuge entwickelt.
Die unsichtbaren Helden des Werkzeug- und Formenbaus verdienen unseren Respekt und manchmal ein bisschen Rampenlicht. Dieser Blick hinter die Kulissen hat gezeigt, wie faszinierend und essenziell ihre Arbeit ist. Es ist eine Mischung aus Kunst und Wissenschaft, aus Tradition und Innovation. Und dank Unternehmen wie PolyTALENT, die die Branche verstehen und unterstützen, können wir darauf vertrauen, dass dieses wichtige Handwerk auch kommende Herausforderungen meistert.
In einer Welt des stetigen Wandels bleiben manche Dinge konstant: Der Bedarf an Präzision, an Kreativität und an Menschen, die im Hintergrund Großes leisten. Werkzeugmacher und Formenbauer werden auch künftig die stillen Helden sein, die unsere Ideen in Form gießen. Ihnen gebührt unser Dank – beim ersten Schluck Kaffee am Morgen ebenso wie beim Blick auf die Skyline moderner Produkte, die ohne sie nicht existieren würden.
Commentaires